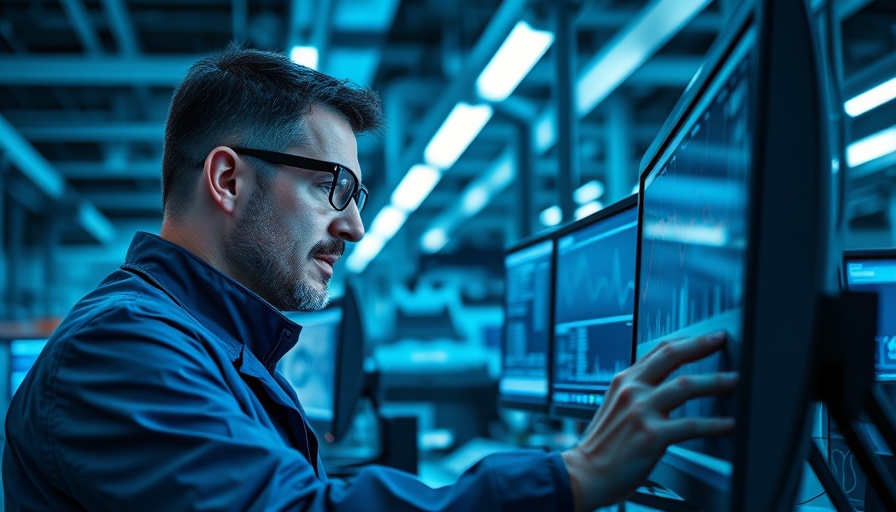
Revitalizing U.S. Manufacturing: A Call to Action
The current revival of U.S. manufacturing faces significant challenges: aging infrastructure combined with an alarming shortage of skilled workers. As reported by the U.S. Chamber of Commerce, over 622,000 manufacturing positions remained unfilled as of early 2024, highlighting a skills gap that could threaten the industrial base. Ivan Madera, CEO of Adaptiv AI, emphasizes that the focus shouldn’t just be on increasing equipment but enhancing the capabilities of the workforce. “We have to find ways to give them the right set of tools so that we can drive productivity up… Otherwise, we’re in trouble,” he warns.
The Generational Shift: Whom Will We Hand It Off To?
Madera points out a stark reality: the average age of machine shop and foundry owners has reached the late 60s to mid-70s. This trend raises the pressing question of succession in an industry desperately in need of rejuvenation. If we fail to bridge this generational gap, we risk creating industrial ghost towns.
Learning from International Examples: Automation Is Not the Sole Solution
Observations from Japan’s automated factories illustrate a vital lesson: automation must complement human skills. Madera recalls visiting a factory where extensive robotics were present, yet bottlenecks stemmed from human inspection tasks that required careful attention. Automation can optimize processes but does not replace the need for skilled operators. This serves as a reminder that as we integrate technology like AI, we must not forget the irreplaceable value of human expertise.
AI as an Amplifier of Human Capabilities: The Future of Work?
The complexity of today's industrial challenges has prompted Madera to propose a transformative role for AI. He envisions AI as a mentor for engineers, using historical data to guide decisions and actions. Such a mentor would not only enhance individual competencies but could also help organizations foresee and mitigate risks that heavily impact production timelines and costs.
Consider a scenario where AI can detect signs of potential disruption in production lines, allowing businesses to adapt swiftly instead of reacting to crises. This capability embodies what Clayton Christensen termed as “seeing around corners,” which empowers companies to stay competitive in constantly shifting markets.
Preparing for the Inevitable Transition: Upskilling the Workforce
As the workforce ages and technology continues to evolve, the need for continuous learning and development will be essential. Companies must invest in training programs that equip employees with skills relevant to emerging technologies like AI and automation. Upskilling can ensure a smoother transition as experienced workers retire, effectively passing down critical knowledge while adapting to new technological realities.
Practical Insights for Business Leaders
Business leaders must adopt an integrated approach that combines technology with human expertise. This could involve establishing partnerships with educational institutions that focus on manufacturing and technology to foster new talent. Additionally, organizations should embrace flexible training methodologies that allow workers to adapt to evolving industry demands, keeping them engaged and productive.
Conclusion: Embrace Change or Risk Obsolescence
As we reflect on the future of U.S. manufacturing, it's clear that adaptation is not merely an option but a necessity. Companies need to revisit their strategies concerning workforce development and technological integration. Only by embracing this change can we hope to revitalize the manufacturing sector, attract a new generation of skilled workers, and secure a robust industrial future.
Are you ready to take action? Invest in training and technology that will help sustain our industrial base and usher in a new era of manufacturing excellence.
Write A Comment