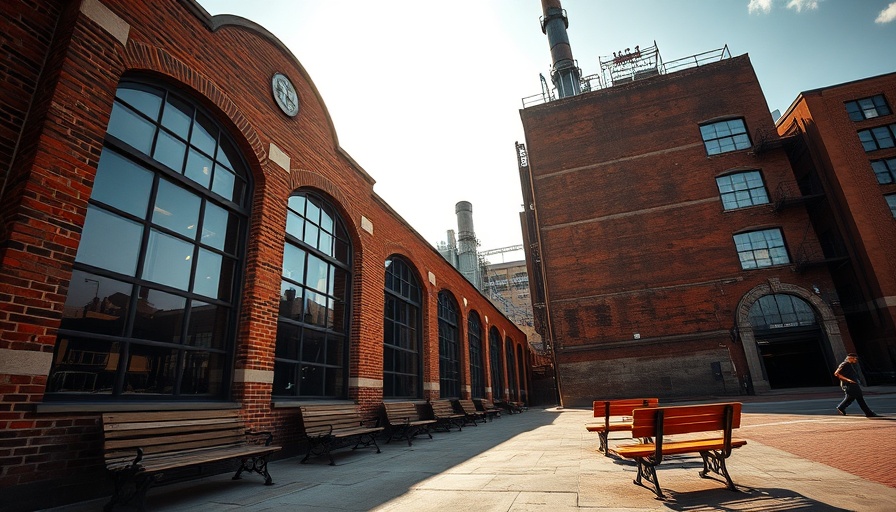
Fire Incident at SPS Technologies: A Safety Wake-Up Call
On February 17, 2025, a significant fire erupted at SPS Technologies’ manufacturing facility in Abington Township, marking an unsettling event in the aerospace industry. The firefighting efforts revealed the complex interplay of safety challenges within advanced manufacturing and raised pressing questions regarding the resilience of research and development (R&D) practices in such hazardous environments.
Understanding the Hazardous Landscape
SPS Technologies, a key supplier of aerospace fasteners including components for iconic vehicles like the Space Shuttle, employs several potentially dangerous manufacturing processes. These procedures involve high-temperature forging, fine metal powder milling, and chemical electroplating, which have previously drawn EPA scrutiny for environmental safety violations. The facility had noted instances of waste management issues and regulatory violations, indicating an uphill battle concerning safety practices.
What Led to the Fire?
The incident, which occurred around 9:30 p.m. ET, reportedly started with an explosion within a warehouse, leading to a blaze that produced dense smoke that local authorities were quick to label as potentially hazardous. Despite the evacuation of all employees and no reported injuries, concerns lingered about the possibility of toxic smoke impacting surrounding communities, prompting the closure of schools in Abington and Jenkintown.
Decoding the Challenges in R&D
The fire reignited long-standing debates about the inherent risks associated with the manufacturing processes involved in producing superalloys—a vital component in the production of high-performance aerospace fasteners. As industries increasingly lean on automated systems to maintain efficiency, questions loom over how these systems can withstand the intense conditions typical of manufacturing environments.
Fire Safety Protocols: Are They Enough?
One of the significant questions posed by this incident pertains to the nature of current safety systems in place for processes involving volatile materials like nickel-based alloys. Historical incidents, such as the 2007 T2 Laboratories explosion, have highlighted vulnerabilities within these processes. As evidenced by SPS Technologies' 2005 EPA fines, the facility's regulatory challenges raise red flags about the adequacy of existing safety protocols.
The Resilience of Automation
A key takeaway from the SPS Technologies incident centers on the resilience of automated systems. Precision plating, automated since the 1970s, was put to the test; however, the inability of emergency systems to contain the blaze early on suggested glaring limitations that need to be addressed within the automation framework. This situation prompts a reevaluation of how industries can better prepare for emergency scenarios to mitigate risks effectively.
Improving R&D to Face Future Challenges
Despite past failures, there are opportunities for innovation in the field of aerospace manufacturing. SPS Technologies has worked on advanced fasteners made from superalloys such as MP35N, MP159, and AEREX 350. Their properties—strength, resistance to corrosion, and stability at high temperatures—underscore the urgent need for continuous research. Future R&D must embrace not only advancements in material science but also improvements in safety procedures and emergency response training.
Conclusion: Reflecting on Safety and Industrial Innovation
The fire at SPS Technologies acts as a critical reminder of the paramount importance of safety in manufacturing environments. As companies push the boundaries in engineering and production, ensuring the integrity of safety protocols becomes essential. For leaders in the industry, this incident is both a lesson and a call to action to foster a culture of safety and accountability, mitigating risks while continuing to innovate.
In light of these challenges, professionals must engage with safety protocols and consider rethinking the approaches to R&D to not only enhance efficiency but also prioritize the safety of employees and surrounding communities.
Write A Comment