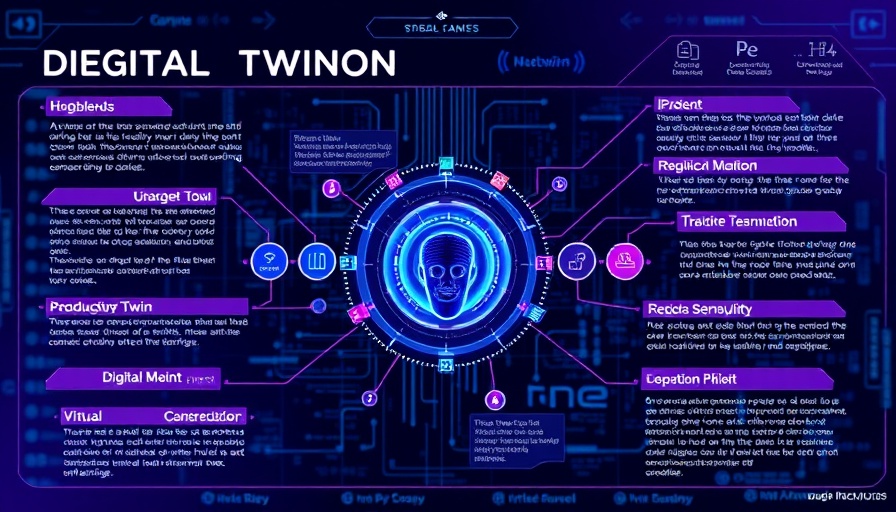
Revolutionizing Steel Manufacturing with Digital Twin Technology
The Digital Twin System for Tapping Process, developed collaboratively by China Steel Corporation and the Industrial Technology Research Institute, marks a significant advancement in steel manufacturing. By leveraging this cutting-edge technology, steel production is becoming more automated and digitalized, which is crucial for maintaining competitive edges in today's high-tech industrial landscape. This innovative system facilitates real-time monitoring, predictive maintenance, and process optimization, ultimately boosting productivity while also reducing costs and enhancing product quality.
The Magic of Real-Time Monitoring and AI Integration
The cornerstone of the Digital Twin model is its ability to precisely replicate equipment operations in real time. This dynamic replication allows continuous condition and data monitoring, which is then meticulously analyzed using sophisticated artificial intelligence (AI) algorithms. The power of this model lies in its predictive capabilities—by foreseeing potential equipment failures, it enables timely preventive maintenance, minimizes downtime, and enhances overall efficiency. The real-time insights provided are crucial for manufacturers seeking to streamline operations while safeguarding against costly production halts.
Optimizing Production Processes Through Simulation
One of the standout features of the Digital Twin system is its capacity to refine production processes significantly. It simulates every phase of operation, from raw material input to product output, thereby automating and optimizing various procedures. This not only assures the quality of the final product but also maximizes production capacity. With enhanced simulations, production waste is reduced, thus promoting a more sustainable use of resources. Additionally, these simulations allow personnel to better grasp production equipment and procedures, fostering a safer and more efficient workplace environment where staff are skillfully prepared for real-world tasks.
Future Implications: What Lies Ahead?
The implications of embracing Digital Twin technology in steel manufacturing extend far beyond present-day applications. As predictive maintenance and process simulations continue to evolve, the future holds the promise of even greater efficiencies and cost reductions. Companies that adopt such technologies can expect to lead the way in innovation within their industries, positioning themselves for future success amid ongoing technological advancements. The trend towards digitization and automation is certain to grow, and those who are well-prepared will be poised to reap the benefits.
Unique Benefits of Adopted Technologies
Understanding and applying digital twin systems in industrial settings provides far-reaching benefits. For businesses, this translates into improved efficiency, higher-quality products, and reduced operational costs. Moreover, the technology empowers employees with deeper insights into production processes and equipment functionality, leading to better-prepared teams. As industries worldwide become increasingly technology-driven, staying informed and up-to-date with such transformative tools becomes a strategic advantage, helping businesses thrive in a competitive market.
Write A Comment